What are the advantages of oil and gas lubrication for rolling bearings?
Oil-gas lubrication, known as “gas-liquid two-phase fluid cooling lubrication technology” in academia, is a new type of lubrication technology. Oil-gas lubrication has incomparable advantages over traditional single-phase fluid lubrication technology. It successfully solves the insurmountable problems of dry oil lubrication and oil mist lubrication, and is a blooming wonderful flower in lubrication technology. It adapts to the needs of the latest development of mechanical industrial equipment, and is especially suitable for harsh working conditions such as high temperature, heavy load, high speed, extremely low speed, and where cooling water and dirt invade the lubrication points.
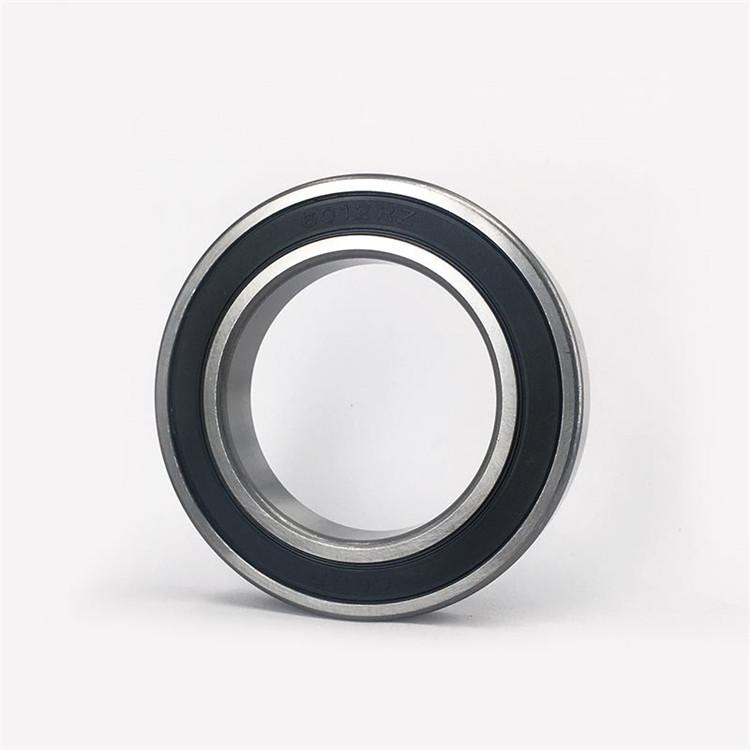
Because oil and gas lubrication can solve problems that traditional single-phase fluid lubrication technology cannot solve, and has very obvious use effects, greatly extending the service life of the friction pair and improving the on-site environment, it is becoming more and more widely used. Especially in the metallurgical industry.
Oil and gas lubrication equipment is suitable for the lubrication of all rolling bearings, especially in harsh industrial and mining environments where transmission parts are operated at high or very low speeds, heavy loads, high temperatures, and corroded by other chemically hazardous fluids. Such as: various types of high-speed wire and bar roll bearings and loopers and guide bearings; various continuous casting machine roll set bearings; various types of cold rolling, hot rolling, and smoothing machine roll bearings, etc.
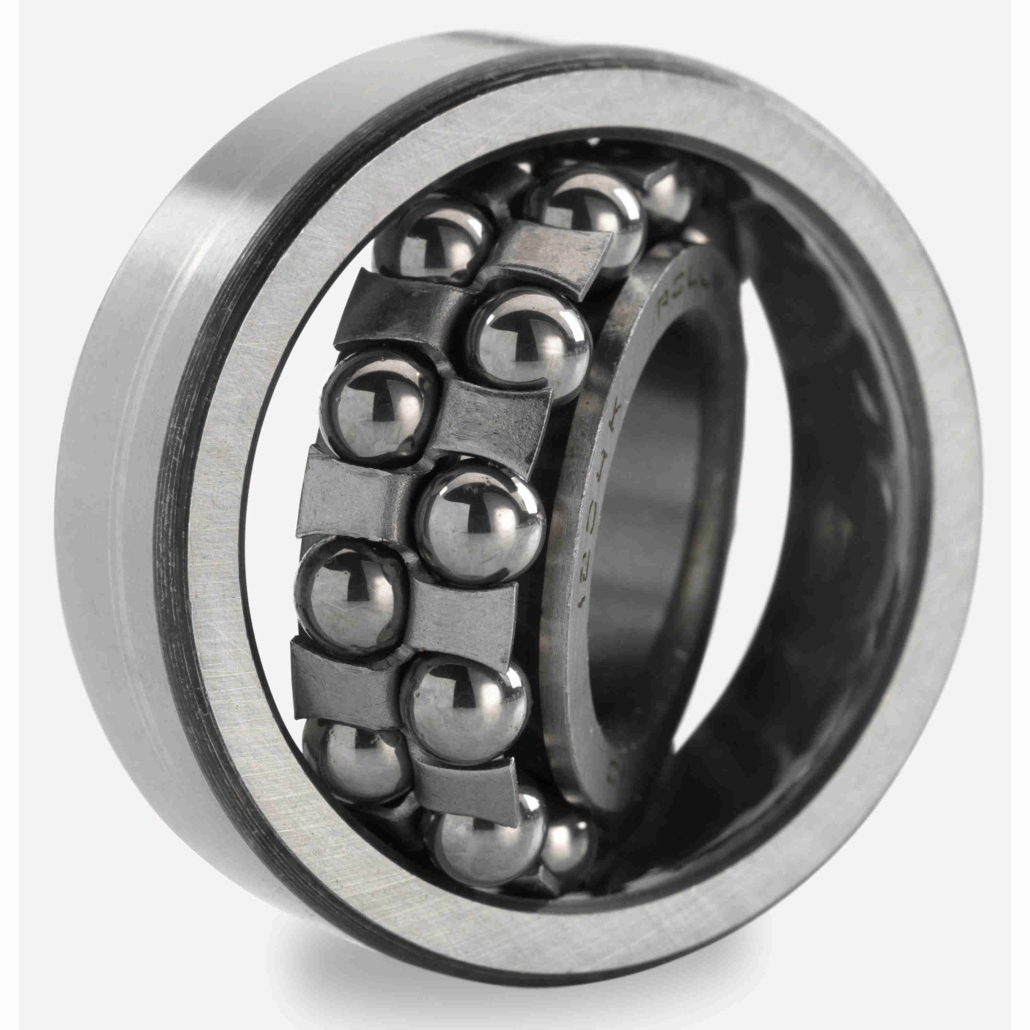
Advantages of oil and gas lubrication for rolling bearings
(1) Oil-gas lubrication is a lubrication method that uses a very small amount of lubricant, avoiding the waste of lubricant, and the lubrication effect is very obvious;
(2) Oil and gas lubrication can maintain a certain positive pressure in the bearing chamber, which can act as a seal to prevent dust and water from penetrating into the bearing seat and causing damage to the bearing;
(3) The compressed air that continuously enters the bearing has a cooling effect on the bearing and prevents the bearing from overheating;
(4) The lubrication condition of the bearing will be significantly improved, and the service life will be greatly extended with the improvement of the lubrication condition;
(5) It avoids the situation that the bearing seat is dirty and difficult to clean when using glycerin lubrication. The inside of the bearing seat is clean while reducing the labor intensity and maintenance cycle of workers;
(6) Avoid contamination of the surrounding environment caused by grease leaking from the bearing seat when dry oil lubrication is used;
(7) Oil-gas lubrication of rolling bearings does not produce oil mist and does not pollute the surrounding air.