What is a needle roller bearing?
Needle roller bearings are roller bearings with cylindrical rollers that are both thin and long relative to their diameter. This type of roller is called a needle roller. Despite its smaller cross-section, the bearing still has a high load-bearing capacity. Needle roller bearings are equipped with thin and long rollers (roller diameter D≤5mm, L/D≥2.5, L is the roller length), so The radial structure is compact. When the inner diameter size and load capacity are the same as other types of bearings, the outer diameter is the smallest. It is especially suitable for support structures with limited radial installation dimensions.
Depending on the application, a bearing without an inner ring or a needle roller and cage assembly can be selected. At this time, the journal surface and shell hole surface matching the bearing are directly used as the inner and outer rolling surfaces of the bearing to ensure the load capacity and operating performance. As with ring bearings, the hardness, machining accuracy and surface quality of the shaft or housing hole raceway surface should be similar to the raceway of the bearing ring. This kind of bearing can only bear radial load.
Features of needle roller bearing:
Needle roller bearings are equipped with thin and long rollers (roller diameter D≤5mm, L/D≥2.5, L is the roller length), so the radial structure is compact, and its inner diameter size and load capacity are the same as other types of bearings. , the smallest outer diameter, especially suitable for support results with limited radial installation dimensions. Depending on the application, a bearing without an inner ring or a needle roller and cage assembly can be selected. At this time, the journal surface and shell hole surface matching the bearing are directly used as the inner and outer rolling surfaces of the bearing to ensure the load capacity and operating performance. As with ring bearings, the hardness, machining accuracy and surface quality of the shaft or housing hole raceway surface should be similar to the raceway of the bearing ring. This kind of bearing can only bear radial load.
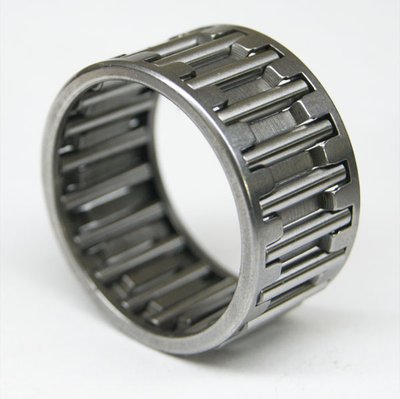
Installation of bearing:
Installation of full complement needle roller bearings is usually carried out using auxiliary sleeves. At this time, the auxiliary roller or auxiliary sleeve holds the needle roller to prevent it from falling out, and the journal lifts the needle roller with its own chamfer. As the needle roller bearing slowly moves inward on the journal, the auxiliary roller Or the auxiliary sleeve will be slowly withdrawn until it is installed in the working position.
The outer diameter of the auxiliary roller and auxiliary sleeve should be 0.1-0.3mm smaller than the shaft diameter. When installing, first apply grease to the inner surface of the bearing outer ring, place the needle roller close to the inner surface (there should be a gap when placing the last needle roller), and then put the auxiliary roller that replaces the journal or the inner ring of the bearing. Or push the auxiliary sleeve into the outer ring hole and align its end face with the end face of the installation shaft or the end face of the inner ring of the bearing installed on the shaft, and then tap with a press or hand hammer to apply pressure.
Needle roller bearings can also be installed by applying a thin layer of lubricating oil to the outer diameter of the auxiliary sleeve and inserting it into the bearing outer ring so that the auxiliary sleeve and the bearing outer ring form an annular hole, and then install the needle roller in the annular hole. After installing the needle roller, use the working shaft to push out the auxiliary sleeve.
For needle roller bearings without an inner ring or outer ring, when installing, first apply a thin layer of grease on the rolling surface of the shaft or housing hole, and place the needle rollers in close contact with the grease at the installation site. There should be a gap when placing the last needle roller. The size of the gap should be 0.5mm on the circumference of the needle roller bearing. Do not force-squeeze the last needle roller in, or install one less needle roller, because when it is hard-squeezed, the bearing will be stuck and unable to rotate; when too little is installed, the gap will be too large, which can easily cause the needle roller to break when the bearing is running. Twist and break. For needle roller bearings with only stamped outer rings, since the outer ring wall is very thin, do not hit it with a hammer for installation, but press it in with a press. Because when hammering with a hand hammer, the pressure is uneven, it is easy to cause local deformation of the outer ring of the needle roller bearing.