Introduction to non-standard bearings
Non-standard bearings refer to bearings that do not meet the external dimensions specified by national standards. They are usually produced according to customer requirements, and the size and structure are not fixed. Non-standard bearings are mainly used in special equipment and special occasions, such as British non-standard bearings, which are mainly customized according to customer requirements and have low versatility.Different from this, ordinary standard bearings are bearings that comply with the external dimensions specified by national standards and are used more widely.
When selecting bearings, appropriate bearings should also be selected based on different application requirements and working conditions. For example, double row angular contact ball bearings are suitable for bidirectional loads, and self-aligning ball bearings are suitable for situations where coaxiality cannot be guaranteed. Tapered roller bearings and deep groove ball bearings can withstand radial and axial loads, etc.
The structural design of non-standard bearings needs to consider factors such as the entry of lubricating oil into the friction surface, the location of the introduction of the bearing, the opening of oil grooves, etc. At the same time, it is necessary to prevent sharp edges or corners that cut off the oil film, and prevent the occurrence of stagnant areas, etc.
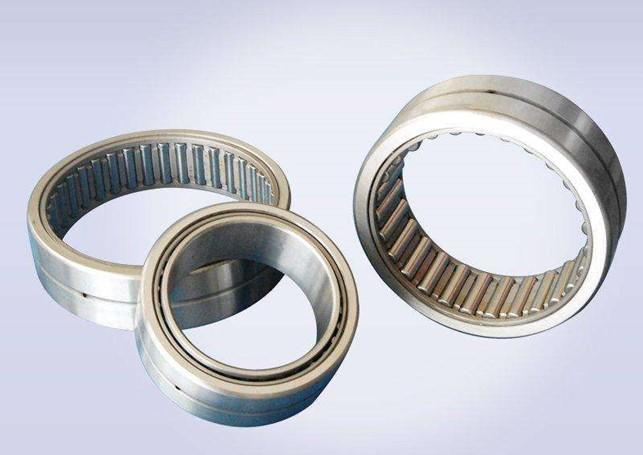
For the production process of non-standard bearings, product design must first be carried out, which requires professional technicians and engineers. During the design process, customer needs and product performance requirements must be fully considered to ensure the feasibility and reliability of the design.
Then, based on the design requirements, the selection and procurement of raw materials begins. The quality of raw materials is directly related to the performance and service life of bearings, so it must be strictly controlled.
After the raw material procurement is completed, the manufacturing and processing of the bearings begin. This process includes heat treatment of bearing steel, turning, grinding and milling of bearing parts, etc. Surface treatment, such as chromium plating, nickel plating, etc., is also required to ensure the appearance and anti-corrosion performance of the bearing.
During the production process, strict quality control measures are essential. In addition to using advanced equipment and processes, such as CNC lathes, grinders, etc., strict quality testing is also required, such as dimensional testing, rotation accuracy testing, fatigue strength testing, etc.
Finally, after the product has been inspected, it is ready for packaging and storage. During the packaging and transportation process, certain measures also need to be taken, such as moisture-proof, shock-proof, drop-proof, etc., to ensure the quality and safety of the product.
To sum up, the production process and quality control measures of non-standard bearings are a systematic and complex process that require all-round control and consideration to ensure that the quality and performance of the products meet customer requirements.