What are insulated bearings?
Insulated bearings are bearings with electrical insulation properties that can effectively prevent the passage of current. They are mainly used in motors, generators and other equipment. This kind of bearing is composed of bearing steel inner ring, outer ring, cage and steel ball (or roller). The rolling elements can be made of ceramics.
In equipment such as motors and generators, rolling bearings may be affected by current erosion, causing bearing damage and motor failure. The use of insulated bearings can effectively prevent the electrical corrosion of the bearings and the influence of grease and rolling elements by current, increase the service life of the bearings, and ensure the normal operation of the equipment.
The electrical insulation properties of insulated bearings can be guaranteed by measuring insulation resistance, shaft voltage and shaft current to ensure that the coating and coating thickness on the bearing surface can withstand the set voltage level.For example, the outer surface of its outer ring or inner ring is coated with a layer of aluminum oxide, which can withstand voltages up to 1000VDC, and its rolling elements are made of ceramics. The insulation condition needs to be measured by measuring insulation resistance, shaft voltage and shaft current. Assure.
Therefore, insulated bearings are widely used in motors, generators and other equipment, mainly to prevent shaft current from causing burn damage to bearings and improve the operating reliability and service life of bearings.
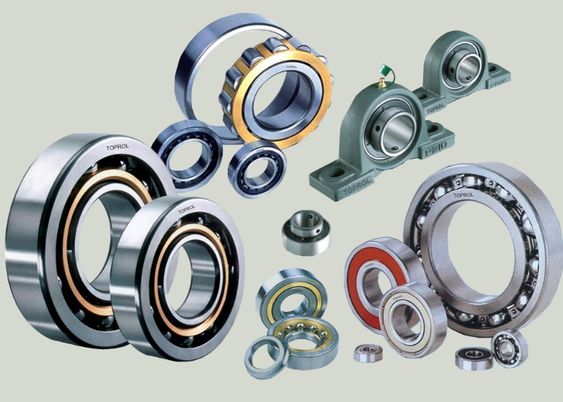
The choice of materials for insulated bearings mainly depends on their function and field of application. In general, these bearings must have high wear resistance, high insulation properties and good mechanical properties.
Common insulating bearing materials include ceramic, graphite and polytetrafluoroethylene (PTFE). Ceramics are known for their high hardness, high wear resistance and good insulating properties. Graphite is widely used in the bearing field due to its low friction coefficient and excellent lubrication properties. PTFE is widely used because of its superior corrosion resistance and insulation properties.
According to different usage environments and working conditions, designers and engineers can also choose other special materials to manufacture insulated bearings. For example, in high temperature, high pressure or extreme environments, you can choose metals with high melting points and good corrosion resistance, such as stainless steel or titanium.
Insulated bearings usually consist of three main parts: the bearing itself, the bushing, and the insulator inside the bushing. Insulators, usually made of materials such as glass or ceramic, are used to isolate the electrical contact between the bearing and bushing. This design ensures the electrical insulation of the sleeve and bearing, allowing the entire device to safely conduct electrical energy during operation.
In practical applications, insulated bearings are often used in power equipment such as high-voltage motors, motors and generators to reduce the risk of corona and leakage. This kind of bearing can also effectively reduce the heat generated in high-speed running equipment and improve its service life and reliability. In addition, the design of the insulated bearings also makes it easy to install and maintain, thus reducing the maintenance cost of the equipment.